Translated from Norwegian from Statoils Alfaposten, written by Tor R. Kristiansen, Lifetime Project:
Emergency fire pumps and control panel replacement
We have now upgraded both emergency fire pumps with new control panels, motor cables and sensors. The first pump FP5020B was upgraded at the beginning of June 2013 and the second pump FP5020A was upgraded in November 2013. The work has been performed professionally with Statfjord A’s own personnel in close cooperation with a highly qualified supplier, and best of all – we saved over 20 MNOK by doing this on our own. But, the story began a few years ago …
Once upon a time …
In February 2009, M1 was notified 40926095: Upgrade emergency firewater pumps, prepared by Geir Haugvaldstad. And in the long text, a total study cost of NOK 750 000 was estimated. The purpose was to boost the reliability of the emergency fire pumps for future service. The study for this project was awarded to Aibel in August 2010. This was a relatively complex task, and eventually silent requirements and ex / non-ex heavy topics were discussed, and the project grew and grew. However, in November 2011 the study was completed and was handed over to Statoil. Further in February 2012, Aibel was given the task of: Upgrade emergency firewater pumps. The cost of the study was approximately 4 MNOK and the implementation was estimated at approx. 24 MNOK. The high execution costs and the scope of work were subject to many internal discussions and proposals to stop the project and implement this on our own, was still mentioned. In spring 2012, Aibel presented a coarse plan that showed just over 2 months of completion per pump, and this was uncomfortable with the tightening we knew would come in WR0213: ‘Action if pumps are out of service’. I sent an e-mail to our production manager Harald Rønneberg, and thought that the risk was higher in carrying out this project than to stop it. I suggested that we carried out the assignment on our own and that I would like Atle Kåsa as operational installation manager (do not know if this job description exists, but it suited us well.) In BMM in June 2012, the project was put on hold and later closed. Our production manager Harald was willing to stand up for our idea, we had convinced him that we would be able to do this on our own. There were many who followed us because this was an unusual way to carry out such a complicated job, but we were never in doubt, we should get this. I contacted Pon Power, which I at that time thought delivered a control panel to the Caterpillar diesel engines, but they referred to Auto-Maskin which was their subcontractor of the control panel.
And here the sunshine story begins …
I contacted Øystein Skogholt at Auto-Maskin and we quickly hit it off. After some telephone conversations, we agreed to visit Auto-Maskin at Skjetten (outside Lillestrøm). On 7 November, a topped A-team left: Atle Kåsa, Kjetil Bergstad, Tommy Axe, Nils Lie and me. Henry Strøm was unable to join us. We were met by Øystein Skogholt, Stig Bredesen and Henning Bredesen from Auto-Maskin.
We had previously submitted pictures and description of the functionality. It was a good meeting. Auto-Maskin came well prepared and had good answers and solutions to problems asked by us. In this meeting I expressed our ambition that we should have such a good plan / preparation that the upgrade per pump should be done in a week. After the visit, A-team agreed that the Auto-Maskin was right for us for this task. Pon Power would also do some replacements of sensors and cables on the diesel engines, but I wanted only one main supplier, Auto-Maskin. Thus Auto-Maskin also took responsibility for Pon Power’s delivery and execution.

Jan Rune Eriksen from Pon Power
In the meeting, we also planned for a site inspection and this was carried out on 11 December with a person from Auto-Maskin and one from Pon Power. In January 2013, a clarification meeting was held with Al and with presentation of the scope / strategy of our implementation. Tore Vikingstad, Kjell Åge Meland and Henry Strøm participated from Al. In the second part of the meeting, we called Øystein Skogly at Auto-Maskin for some clarifications. And after the meeting, we were given permission to proceed as planned. At the end of January 2013, we received offers according to our specifications, and in mid-February we sent the order. FAT was performed and approved 24 April. Participants from our site were: Henry Strøm, Kjetil Bergstad, Atle Kåsa and Nils Lie. As the final preparation before sending equipment and parts, a meeting was held at Auto-Maskin 13 May where I attended. The purpose of the meeting was to ensure that all details were in place and review our requirements and expectations for HSE. The goods were sent to CCB the day after. Then it was ready for replacement of panels, cables and sensors on the first emergency fire pump FP5020B. The job started 29 May and was completed and tested 7 June.
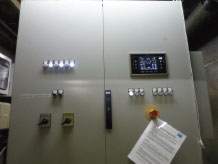
This is what the new control panel looks like.
An impressive job was done by: Atle Kåsa, Nils Lie, Henry Strøm and Stig from Auto-Maskin and Andreas from Pon Power. But there are many who have contributed in this process and deserve praise: Frank Kåre Eriksson, Kjetil Bergstad, Helge Erdal, Tommy Axe and excellent service from the D & V and PV departments. Training of operating personnel and preparation of operating instructions was done in parallel to the installation, and the necessary operational expertise was forwarded to all shifts. The feedback after this was very positive. Replacement of the next emergency fire pump panel was scheduled for September, and I attended a preparatory meeting at Auto-Maskin 29 August for review of experience and improvements. Due to tightening in WR0213, coordination against heavy workload aboard and not least shift plans for Nils Lie and Atle Kåsa, the replacement job was scheduled for 18 November 2013. The implementation of FPS020A, went brilliantly! The job started 19 November and the successful test run was performed on 25 November.
Why did this work so well?
- Our production manager Harald Rønneberg believed in us and was willing to ‘fight’ for the task to be performed in this way, this was of course absolutely crucial and motivated us.
- Al by Tore Vikingstad and Henry Strøm approved our plans and Henry later became a key person for us. We had Nils Lie as FA Elektro on land and he has a passion for such challenges and did a great job.
- We had the right people with the right skills and the desire to achieve this.
- We always had direct contact with our main supplier and things were quickly clarified and coordinated along the way. Auto-Maskin impressed us with their down to earth attitude, professional competence and reliable follow-up.
- Of course, the platform was with us the whole way, and I attach the closing mail from ‘Operational Installation Manager’ Atle Kåsa who sums it up nicely:
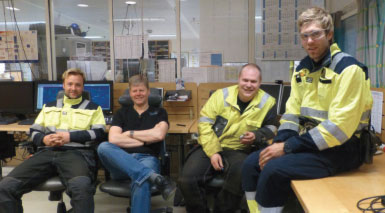
From left: Stig Bredesen (Auto-Maskin), Atle Kåsa (FA operations), Andreas Lundgård (Pon Power) and Nils Lie (FA electro)
“Hi! Now the control panel for emergency fire pump A is completed and emergency fire pump B has been fitted with the remaining sensors and transmitters. All tests show that both fire pumps are working properly. Labeling of cables and transducers / transmitters remains on both emergency fire pumps, but Nils will take care of this on his next trip out. Nils and Stig quality assured drawings and verified labeling of cables and encoders and transmitters one last time before they left. In my group, a very good job was done. Nils (electro), Stig (Auto-Maskin) and Jan (Pon Power) have really been at it every single day. Great job! Pon Power got some criticism for the job on the B-pump, but this time they deserve praise. Pål and Arild from Mechanical, Asbjørn and Odd Eirik from automation always came on short notice when the need was there. A big thank you to them. The welder from Aibel and the insulator guy from Beerenberg came at once when we needed assistance. They should also be praised for their effort. With so many serviceminded and skilled people, it is a pleasure to do such jobs here on Statfjord A.”